EVALUATION OF COMPOSITE MATERIAL CHANGE OF AN AIRPLANE SEAT LEG
About
During the course of this project, an airplane seat leg was modeled using Solidworks and a material model was generated using Digimat-MF for a Grivory GV-5H (PA66 matrix reinforced with 50% Glass Fibers).
The experimental curves of Grivory GV-5H material was loaded in Digimat-MX and reverse engineered to generated the true stress vs true strain curves.
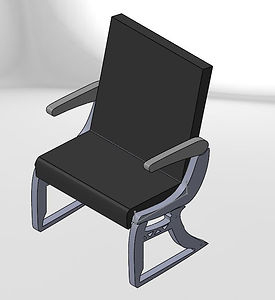


CAD MODEL OF THE PART
A CAD model of the airplane seat leg was designed using Solidworks. The part was designed keeping in mind the FAA requirements such as sustaining the 9g forward loading test.
AUTOMATIC METHOD CALIBRATION
The Grivory GV-5H experimental curves from Digimat MX were used to calibrate an elasto-plastic material model using automatic method.
INTERACTIVE METHOD CALIBRATION
Using the interactive calibration method, the material model was optimized to curve fit the experimental curves with the acquired True Stress-True Strain plots.