COREBACK TOOLING FOR NANO CELLULAR FOAM INJECTION MOLDING

About
Coreback tooling strategy is used for foam injection molding of plastic components.
A Super Critical Fluid (SCF) is mixed with molten material to form a homogeneous mixture which is then injected into a mold cavity. One side of the mold cavity is retracted at a very high rate which causes a sudden pressure drop inside the mold leading to the nucleation of foaming bubbles in the plastic part.
I worked in developing the tool structure design and worked in the simulation of this coreback injection molding manufacturing process using Moldex 3D mold filling simulation software.
COREBACK TOOL ASSEMBLY

Worked with the tooling structure involved in coreback injection molding manufacturing to attain nano-cellular foamed specimen.
COREBACK TOOLING STRATEGY

Coupling of foam injection molding (FIM) process with coreback tooling strategy helps us achieve higher volume expansions when compared to conventional FIM.
Before manufacturing this tool, we have set up a similar model in Moldex 3D to analyze the effect of various process variables in the cell morphology of the manufactured part.
CELL MORPHOLOGYÂ SIMULATION RESULTS
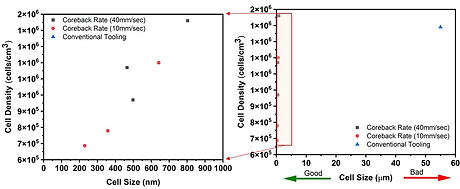
Acquired the cell size and cell density results from Moldex 3D.
Some of the process variables of Coreback Injection Molding are:
-Coreback Rate
-Coreback Distance
-Dwell Time (Delay Time)
Key Takeaways
Faster coreback rate with increasing dwell time gives much less time for bubbles to nucleate, leading to lesser cell density results.
Cell nucleation begins only during the expansion of the coreback tool and hence there is very less cell size at extended dwell times.
Advantages
Coupling of foam injection molding (FIM) process with coreback tooling strategy helps us achieve higher volume expansions when compared to conventional FIM.
Before manufacturing this tool, we have set up a similar model in Moldex 3D to analyze the effect of various process variables in the cell morphology of the manufactured part.
Conclusion
With established manufacturing to response pathway for Foam Injection Molding, we are moving ahead with a similar simulation approach for the core-back tooling strategy before manufacturing the tool. This helps us streamline the initial tool trials.